Diamond grinding wheel is the hardest grinding wheel, with "invincible" ability, grinding ability is very strong, but we must pay attention to some problems when using the diamond grinding wheel,so that can extend the life of diamond grinding wheel.
1. Diamond grinding wheel is a valuable diamond tool for processing high hardness materials, but not suitable for grinding ordinary steel or other soft materials.
2. After assembled with flange, the diamond grinding wheel must be quietly balanced before use. Do not remove the flange until the grinding wheel has run out.
3. The spindle selection accuracy of the grinding wheel machine is high (radial run-out is not greater than 0.01 mm), can be used as a micro-level intron.
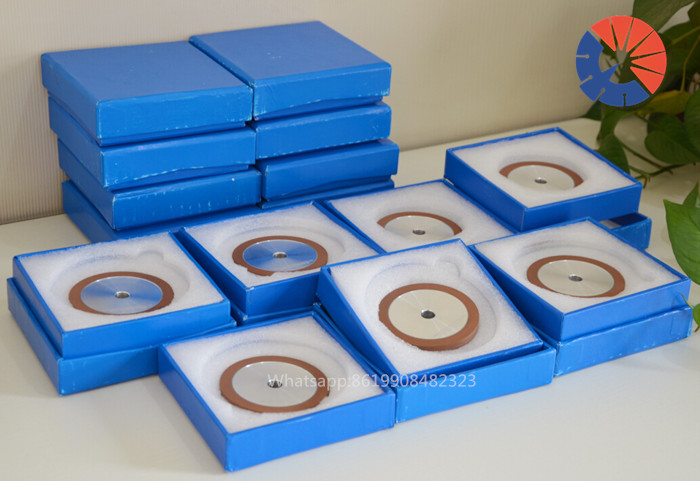
4. The appropriate grinding dose must be selected. The following data are available for reference:
(1) Line speed of diamond grinding wheel:
Metal bond: 110/15/s (dry grinding), 220/35/s (wet grinding)
Resin bond: 115/30/s (dry grinding), 225/40/s (wet grinding)
(2) The workpiece line speed is generally 10≤15 m/min.
(3) Grinding depth: grinding depth should be small,or the grinding efficiency is not high because of the high wear speed. Generally speaking, 0.005mm/oxygen stroke is appropriate. The finer the particle size , the smaller the grinding depth, especially when coolant is not used.
(4) Longitudinal forward speed: typically 10≤15 m/min.
5.Coolant should be used as much as possible during grinding, which can not only improve grinding efficiency and grinding quality, but also reduce grinding wheel wear. Commonly used coolants are kerosene, light diesel, light engine oil lamps, kerosene is the best.
6.When using the new diamond grinding wheel, in order to obtain the correct shape (outer roundness, flat face), it is also required to use silicon carbide grinding wheel or silicon carbide abrasives on the metal plate or glass plate manual grinding (for dressing the grinding wheel end face).